Les bonnes pratiques d’entretien préventif et curatif adaptées à la gestion thermique
Face aux défis imposés par la chaleur sur les équipements agroalimentaires, l’entretien joue un rôle crucial pour préserver la performance, la sécurité et la durabilité des installations. Mettre en place des stratégies de maintenance adaptées aux conditions thermiques extrêmes permet de limiter les risques de pannes, d’optimiser les coûts d’exploitation et d’assurer une production stable et conforme aux exigences …
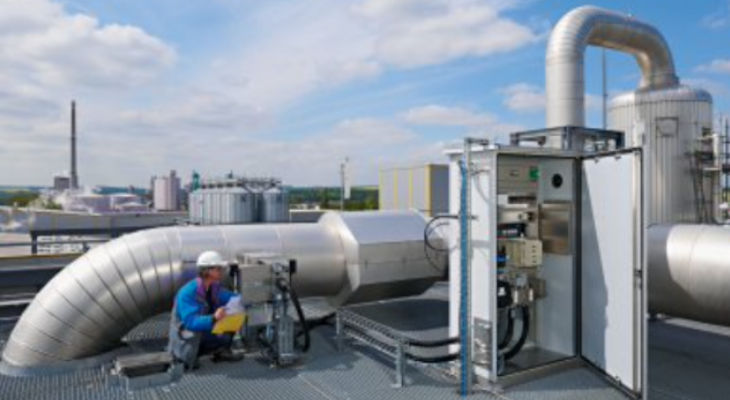
Face aux défis imposés par la chaleur sur les équipements agroalimentaires, l’entretien joue un rôle crucial pour préserver la performance, la sécurité et la durabilité des installations. Mettre en place des stratégies de maintenance adaptées aux conditions thermiques extrêmes permet de limiter les risques de pannes, d’optimiser les coûts d’exploitation et d’assurer une production stable et conforme aux exigences sanitaires. Voici les bonnes pratiques, outils et méthodes qui doivent être adoptés pour anticiper et gérer au mieux les effets délétères de la chaleur.
Établir un plan de maintenance spécifique à la chaleur
La première étape consiste à intégrer la gestion thermique dans le plan global de maintenance de l’usine. Cela implique d’identifier les équipements les plus exposés aux températures élevées et d’adapter la fréquence des contrôles en conséquence. Par exemple, les moteurs, pompes, échangeurs thermiques, ainsi que les systèmes électriques sensibles doivent faire l’objet d’inspections plus régulières pendant les périodes critiques.
Un calendrier d’entretien préventif doit être défini, avec des actions cibléescomme le nettoyage des ventilations, le remplacement des filtres, le contrôle des systèmes de refroidissement et la vérification des joints et lubrifiants. Ces actions permettent d’éviter l’accumulation de poussières ou de résidus qui favoriseraient la surchauffe, et de garantir une dissipation thermique efficace.
La maintenance préventive, un levier clé contre la dégradation thermique
La maintenance préventive vise à anticiper les défaillances avant qu’elles ne surviennent. Dans un contexte de chaleur, elle inclut des interventions spécifiques :
– Lubrification adaptée : Les lubrifiants traditionnels peuvent perdre leur efficacité à haute température. Il est essentiel d’utiliser des produits adaptés, capables de résister à des plages thermiques élevées, pour éviter l’usure prématurée des pièces mobiles.
– Surveillance des systèmes de refroidissement : Radiateurs, ventilateurs, circuits d’eau froide ou de fluide caloporteur doivent être vérifiés régulièrement pour garantir un fonctionnement optimal. Tout dysfonctionnement peut rapidement entraîner une surchauffe.
– Nettoyage et dépoussiérage : La chaleur accentue l’accumulation de poussières et de débris, qui agissent comme isolants thermiques. Un nettoyage rigoureux et régulier des surfaces, des filtres et des grilles d’aération est indispensable.
– Contrôle des isolants et joints : Ces éléments, soumis à des cycles thermiques répétés, peuvent se fissurer ou durcir. Leur état doit être contrôlé et leur remplacement anticipé pour éviter des fuites ou infiltrations.
La surveillance technologique et les outils d’analyse
Les outils modernes permettent d’affiner la gestion de la maintenance en contexte thermique. L’intégration de capteurs de température sur les équipements clés offre une surveillance en temps réel, avec alertes en cas de dépassement des seuils critiques. Couplés à des systèmes d’analyse de données, ces capteurs facilitent la maintenance prédictive, en détectant les anomalies thermiques avant qu’elles ne causent des pannes.
L’analyse vibratoire est également un indicateur précieux : une surchauffe peut modifier les vibrations émises par un moteur ou un roulement, signalant un dysfonctionnement imminent. Des inspections thermographiques, réalisées avec des caméras infrarouges, permettent par ailleurs de visualiser les zones chaudes et de détecter les points faibles invisibles à l’œil nu.
Un autre levier essentiel est la formation des opérateurs et techniciens à la problématique thermique. La compréhension des effets de la chaleur sur les équipements et des gestes adaptés à adopter en situation de forte température est un facteur clé de réussite. Les équipes doivent être sensibilisées aux bonnes pratiques, comme la vérification régulière des dispositifs de refroidissement, la manipulation prudente des machines surchauffées, ou encore la gestion des cycles de production.
Cette formation contribue aussi à instaurer une culture proactive de la maintenance, où les anomalies sont signalées rapidement et les interventions planifiées avec rigueur.
Protocoles d’intervention curative en cas de surchauffe
Malgré toutes les précautions, des incidents liés à la chaleur peuvent survenir. Il est donc indispensable de disposer de protocoles d’intervention clairs à savoir un arrêt sécurisé des équipements; un diagnostic précis qui permet d’identifier la cause exacte du problème, qu’il s’agisse d’un défaut de lubrification, d’un encrassement ou d’une défaillance électrique ; la réparation et le remplacement ciblés ; et une revue des procédures.
De nombreuses entreprises agroalimentaires ont mis en place avec succès ces bonnes pratiques. Par exemple, certaines ont adopté des systèmes de capteurs intelligents pour surveiller en temps réel la température des moteurs critiques, réduisant ainsi les arrêts non planifiés de plus de 30 %. D’autres ont revu leur calendrier d’entretien en fonction des saisons, renforçant les contrôles pendant les mois les plus chauds, avec des résultats probants sur la durée de vie des équipements.
Dans certains cas, la formation continue des équipes a permis d’améliorer la réactivité face aux signes précurseurs de surchauffe, évitant ainsi des pannes coûteuses.
Connectez-vous avec vos réseaux sociaux :