Métrologie : Les enjeux du pilotage par la mesure
La métrologie, souvent reléguée à l’arrière-plan dans les discours sur la performance industrielle, joue pourtant un rôle de premier plan dans le secteur agroalimentaire. Loin de se limiter à une série de contrôles ponctuels, elle est aujourd’hui un maillon essentiel de la chaîne de valeur, garantissant la conformité des produits, leur sécurité sanitaire et leur homogénéité. Dans une industrie …
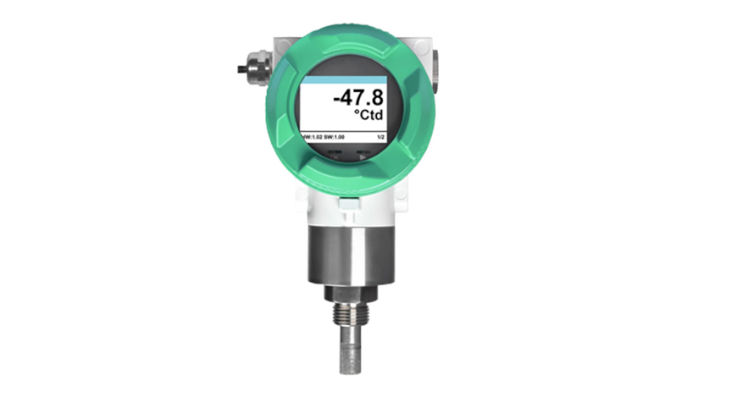
La métrologie, souvent reléguée à l’arrière-plan dans les discours sur la performance industrielle, joue pourtant un rôle de premier plan dans le secteur agroalimentaire. Loin de se limiter à une série de contrôles ponctuels, elle est aujourd’hui un maillon essentiel de la chaîne de valeur, garantissant la conformité des produits, leur sécurité sanitaire et leur homogénéité.
Dans une industrie soumise à des normes strictes, comme les référentiels ISO 22000, IFS Food ou BRC, la fiabilité des mesures conditionne directement la capacité d’une entreprise à répondre aux exigences des autorités de contrôle, mais aussi à celles des distributeurs et des consommateurs.
Sur le plan de la qualité produit, la métrologie permet d’atteindre une régularité cruciale. Mesurer précisément la teneur en sel, en matières grasses ou en humidité, c’est éviter les écarts de goût, de texture ou de conservation. Dans un secteur où le moindre défaut peut entraîner un rappel de lots coûteux et entacher l’image de marque, l’exactitude des mesures devient un facteur de différenciation.
Au-delà de la qualité, les systèmes de mesure et de régulation contribuent aussi à l’optimisation des procédés industriels. Grâce à des données fiables, les lignes de production peuvent ajuster automatiquement les paramètres de fabrication, limitant les pertes de matières premières, réduisant les consommations énergétiques et minimisant les rebuts. Ce pilotage par la donnée permet aux industriels de gagner en efficacité tout en respectant leurs engagements environnementaux, dans un contexte où la sobriété énergétique devient un critère de compétitivité.
Enfin, la métrologie est indissociable de la traçabilité, exigence majeure dans l’agroalimentaire. Chaque mesure, qu’elle concerne une température, un débit ou un niveau de CO₂, participe à la constitution d’un historique fiable, indispensable pour reconstituer les conditions de fabrication d’un lot en cas d’alerte sanitaire. Elle devient ainsi un outil de maîtrise des risques, mais aussi un élément de preuve en cas d’audit ou de litige.
Une diversité d’instruments de mesure au service de la qualité
Pour répondre à ces enjeux multiples, l’industrie agroalimentaire s’appuie sur une large gamme d’instruments de mesure, adaptés à chaque étape du processus de transformation. Ces outils, souvent intégrés dans des systèmes automatisés, jouent un rôle de sentinelles invisibles, surveillant en permanence les paramètres critiques.
Les mesures physiques restent les plus courantes. La température, par exemple, est surveillée tout au long du cycle de production (du stockage des matières premières à la cuisson, en passant par le refroidissement et le transport), afin de garantir le respect de la chaîne du froid ou les seuils de pasteurisation. La pression, l’humidité relative, le niveau dans les cuves ou encore le débit des fluides sont également suivis de près pour assurer la stabilité des processus.
À ces données s’ajoutent les mesures physico-chimiques, qui permettent un contrôle plus fin des caractéristiques des produits. Le pH, la conductivité, la turbidité ou encore la teneur en sucre (mesurée en degrés Brix) sont autant d’indicateurs déterminants pour la qualité organoleptique et microbiologique des aliments. Par exemple, dans les boissons sucrées ou les confitures, un écart de quelques degrés Brix peut altérer à la fois le goût et la conservation.
L’évolution des technologies a également permis l’essor de systèmes de mesure microbiologiques automatisés. Ces dispositifs, basés sur des principes comme la spectroscopie infrarouge, la fluorescence ou l’absorption optique, offrent une détection rapide des contaminants sans passer par une culture classique en laboratoire. Dans les lignes de production à haut débit, ces instruments permettent un contrôle en temps réel et une réactivité accrue.
Enfin, les instruments eux-mêmes sont en pleine mutation. Les balances deviennent intelligentes, les capteurs se miniaturisent et gagnent en précision, tandis que la connectivité s’impose comme un standard. Grâce à l’Internet des objets (IoT), de nombreux équipements sont désormais capables de transmettre automatiquement leurs données vers un système centralisé (ERP, MES ou SCADA), facilitant leur exploitation et leur archivage. Cette intégration numérique ouvre la voie à une métrologie connectée, proactive et mieux alignée sur les impératifs industriels contemporains.