Viande : Vers une traçabilité totale dans les usines de transformation avec la RFID
La sécurité et la traçabilité alimentaires sont des sujets de première importance pour les producteurs, fournisseurs et clients finaux. Des directives comme le règlement (CE) 178/2002 de l’Union Européenne et la disposition 9 CFR du Département de l’Agriculture des États-Unis imposent à leurs membres des procédures de sécurité alimentaire obligatoires. Cela étant, ces réglementations ne couvrent que très peu …
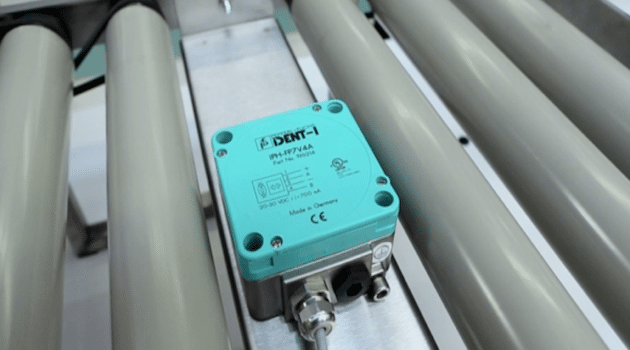
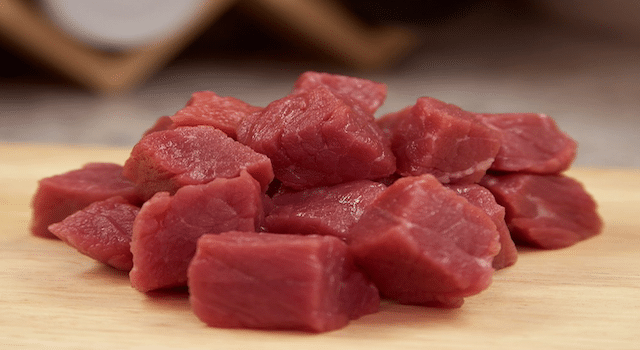
La sécurité et la traçabilité alimentaires sont des sujets de première importance pour les producteurs, fournisseurs et clients finaux. Des directives comme le règlement (CE) 178/2002 de l’Union Européenne et la disposition 9 CFR du Département de l’Agriculture des États-Unis imposent à leurs membres des procédures de sécurité alimentaire obligatoires.
Cela étant, ces réglementations ne couvrent que très peu la question de la traçabilité interne. À ce stade de la production, des avantages de sécurité notables peuvent être développés. Par exemple, il peut s’agir de collecter davantage de données, ce qui entraînera des améliorations substantielles en termes de commande des procédés et de gestion des stocks. Des campagnes de rappel mieux ciblées peuvent en outre être mises en place comme l’explique pepperl-fuchs, leader comme concepteur et fabricant de capteurs et composants électroniques pour le marché mondial de l’automatisation.
L’une des plus grandes entreprises de transformation de la viande au monde, implantée en Europe, a ainsi atteint une traçabilité complète de la viande traitée dans ses usines de production, grâce à la technologie RFID de Pepperl+Fuchs explique le groupe.
Son usine de transformation du porc peut traiter à elle seule jusqu’à 90 000 animaux par semaine. Un système de convoyage transporte le bétail, avec un transpondeur intégré à chacun des crochets de transport. Une identification précise est ainsi possible sur toute la chaîne de production. L’occasion de revenir sur cette technologie pas toujours bien intégrée…
Un stockage d’informations uniques dans les transpondeurs
Comme l’explique Pepperl+Fuchs, le système RFID doit pouvoir résister aux gammes de température extrêmes comprises entre -30 °C et 140 °C rencontrées pendant les différentes étapes du processus. En plus de satisfaire les exigences en termes de distances de lecture et de vitesse de déplacement prévues, les transpondeurs doivent atteindre une durée de service d’au moins cinq ans. Les appareils de lecture doivent par ailleurs résister aux environnements difficiles de l’industrie agroalimentaire.
Grâce au stockage d’informations uniques dans les transpondeurs RFID, des données relatives aux produits sont collectées et documentées à chaque point de traitement. Les données à collecter incluent le poids, la taille, l’épaisseur de la couche de graisse et, bien entendu, le fournisseur en amont. Les résultats des examens vétérinaires s’ajoutent à ces informations. Au cours de ce processus, ces données sont systématiquement associées à un animal spécifique.
Adapté aux environnements difficiles de l’industrie de transformation de la viande
Une fois les exigences du client identifiées, un système RFID basse fréquence a été choisi. Des transpondeurs IPC02-16 et IPC11-12 ont été intégrés directement au métal des crochets des convoyeurs. Dans une deuxième application de l’usine, ces transpondeurs sont utilisés sur des racks «arbre de Noël » permettant de charger les découpes de viande dans les camions frigorifiques. Pour cette opération, les transpondeurs sont utilisés en tant que clips pouvant être détachés de leur rack avant l’expédition, ce qui permet leur réutilisation. Dans un troisième temps, les transpondeurs RFID sont utilisés sur des boîtes de transport en plastique déplacées par des convoyeurs à rouleaux. Les découpes de viande sont acheminées vers des points de traitement supplémentaires équipés de transpondeurs IPC11-50CD. Ces transpondeurs sont placés au fond de la boîte. Il est possible de les lire à une distance maximale de 80 mm.
Des têtes de lecture RFID IPT-FP utilisées pour lire les informations
Pepperl+Fuchs propose pour ces appareils des coffrets en acier inoxydable, particulièrement adaptés aux environnements difficiles de l’industrie de transformation de la viande. Auparavant, une interface Profibus était utilisée. Au fil du temps, une interface Profinet a été adoptée pour ce processus. Puisque Pepperl+Fuchs fournit des produits capables d’interagir avec tous les types de protocoles de communication et de bus de terrain industriels courants, ce changement n’a posé aucun problème. Actuellement, des têtes de lecture/d’écriture RFID IPH-FP7V4A sont employées conjointement à l’interface IDENTControl.
Pour un maximum de flexibilité, Pepperl+Fuchs a fourni des lecteurs portatifs pouvant être programmés en JavaScript et capables de lire correctement les formats de données spécifiques. Les transpondeurs programmables 40 bits permettent au client d’ajouter des codes personnalisés à chaque étiquette.
Par ailleurs, grâce à la fonction de programmation unique (OTP, One Time Programmable) un code fixe ne pouvant pas être modifié, ou « fixcode », peut être généré. Les lecteurs portatifs peuvent être configurés spécifiquement pour satisfaire ces exigences.
Les avantages de la technologie RFID
L’utilisation de la technologie RFID fournie par Pepperl+Fuchs procure aux abattoirs des avantages intéressants en termes de traçabilité et de suivi alimentaires, étant donné qu’elle offre une détection sans contact et entièrement automatisée sur toute la chaîne de production. Les transpondeurs sont résistants à la contamination, aux variations importantes de température et aux changements du taux d’humidité. Cette technologie d’identification ne nécessite donc presque aucune maintenance.
Les transpondeurs RFID permettent également de recevoir et de stocker des informations pendant le processus. S’agissant d’éléments passifs, ils n’ont besoin d’aucune alimentation supplémentaire. Aujourd’hui, le client exploite 600 systèmes d’identification et 30 000 transpondeurs RFID dans son usine de traitement centrale, qui lui procurent une traçabilité et un suivi de la viande en interne, sécurisé et entièrement automatisé.
Connectez-vous avec vos réseaux sociaux :